ldpe autoclave vs tubular|qenos autoclave ldpe : China Good control on molecular properties, and as a consequence on end-use properties, is very important for low-density polyethylene (LDPE) manufacturers. However, the connection between the architecture of polymer chains and the kinetic mechanism and polymerization conditions is still a subject of study. In this work, we present a comprehensive . leaching autoclave systems provides the ideal solution for the safe, reliable removal of ceramic cores with a range of units designed to suit the application or production quantity.
{plog:ftitle_list}
Geeta Industries | Surgical Equipment And Dairy Equipment - Manufacturer of Surgical Equipment, Dairy Milk Can and Bulk Milk Cooler from Jagadhri
Figure 3.3 shows a comparison between the tubular grades and the most common autoclave grades for extrusion coating 2404AN00 (MFR: 4.2 g/10min), 1808AN00 (MFR: 7.5 g/10min) . Good control on molecular properties, and as a consequence on end-use properties, is very important for low-density polyethylene (LDPE) manufacturers. However, the connection between the architecture of polymer chains and the kinetic mechanism and polymerization conditions is still a subject of study. In this work, we present a comprehensive .
of low density polyethylene (LDPE) and ethylene vinyl acetate (EVA) copolymers. The Lupotech T process is the leading high pressure tubular reactor technology for the production of LDPE and standard EVA, while Lupotech A is the high-pressure autoclave reactor process technology for the production of specialty LDPE, EVA copolymers with very
lames emboitables autoclave
Autoclave vs. Tubular LDPE Current knowledge: • Broad MMD and LCB is essential for NI and web stability • Typical Autoclave grade behaviour; Low NI, stable film web r a l ubu Tl ac i py•T grade behaviour; Large NI, unstable film web chill roll film web die Extruder. 1.3 Paper 7651 Marcel Neilen 11Gela Plant (Italy) 130 - LDPE 1981 Umm Said Plant (Qatar) 180 - LDPE 1996 Dunkerque Plant (France) 240 – LDPE/EVA 2011 (Autoclave converted to tubular) Location Capacity (kt/y) 1st start up date Gela Plant (Italy) 70 - LDPE 1963 Ferrara Plant (Italy) 110 - LDPE 1976 Maracaibo Plant (Venezuela) 70 - LDPE 1976 Bratislava Plant (Slovakia) 90 .Polymer Testing 9 (1990) 341-351 Morphological Characterization of Autoclave and Tubular LDPE by High Temperature IR Spectroscopy* G. C. Pandey, B. P. Singh & A. K. Kulshreshtha$ Research Centre, Indian Petrochemicals Corporation Ltd, Vadodara-391 346, Gujarat, India (Received 6 January 1990; accepted 19 April 1990) ABSTRACT High temperature IR . LDPE can be produced by different types of autoclave or tubular reactors, which can also be cascaded. An important effort is to obtain materials with autoclave-process equivalent properties from tubular technology due to economic reasons. In this way, the molecular understanding of the materials attains a key role.
shows the simplified industrial production of LDPE using autoclave reactor (left) and tubular reactor (right). Autoclave reactor is a stirred cylindrical reactor typically about 6.1 m long and 0.38 - 0.91 m in diameter. Tubular reactor is similar to a tube or long pipe which usually about 1.25 km long and 2.5 - 7.6 cm in diameter.
qenos autoclave ldpe
The tubular reactors operate at pressure up to 3,000 bar, whereas Autoclave reactor operates below 2,000 bar. MI range: 0.2 – 150 . Product from the tubular process is typically higher in molecular weight and has more short chain branches than LDPE from the autoclave process . Produce LDPE homo-polymers and ethylene vinyl acetate (EVA .While most of the newly installed LDPE/EVA capacities are based on tubular reactors, autoclave reactors are still relevant, especially for producing specialty-grade EVAs. This report reviews the technology and evaluates the process economics for producing EVAs with a high-pressure autoclave reactor process and a high-pressure tubular reactor .
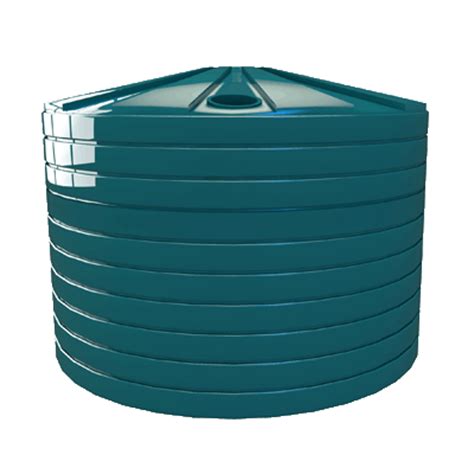
Autoclave Tubular Figure 1: Normalized molecular weight distribution plots for an autoclave and a tubular LDPE resin. The conformation plot shows the mean radius of gyration as a function of the molecular weight. Figure 2 shows an example for a HDPE, an autoclave LDPE and a tubular LDPE. The typical upward curl below 105 g.mol-1 is an For tubular processes, estimates are developed for LDPE and EVA (18% VA), while for autoclave processes, estimates are developed for LDPE and EVA (18% VA and 28% VA). In each region, the technology (tubular versus autoclave) employed affected the relative cost of production. View table of contents
Autoclave vs. Tubular LDPE: A Thai Perspective 🇹🇭 In the world of Low-Density Polyethylene (LDPE), two primary production processes dominate: Autoclave and Tubular. These processes give LDPE .
LDPE was discovered by ICI in 1933 →autoclave process in 1938 BASF developed the first tubular process during WW II High variation of autoclave and tubular processes by different licensors Nowadays licences available up to 400 kt/y plant capacity Consumption in 2015 –Global: 20,5 million t –Domestic: 60-65 thousand t MPK (TVK) LDPE plantsAutoclave vs. Tubular Process Autoclave Conversion up to 21% - adiabatic, reaction heat removed by reactant only 1300-2000 bar operating pressure Higher capacity of hyper compressor Organic peroxide initiators only Specialty polymer capability – EVA copolymers over 40% vinyl acetate Lower reactor capacity – 150 kt/y Tubular
This paper discusses the general chemical and rheological differences between autoclave and tubular LDPE resins then focuses in more detail on those differences for a variety of tubular LDPE .
Lo w-densit y p oly eth ylene (LDPE) is without a doubt one of the most widespread p olymers w orldwide. Its ann ual pro duction is estimated at 24 million tonnes and it is used for a large n um b er of applications, e.g., pac kaging, adhe-siv es, insulators, coatings and lms. Most of the LDPE is no w ada ys pro duced in tubular reactors, whic .LDPE Tubular reactor vs Autoclave reactor: Autoclave reactor: -- conversion up to 21% --adiabatic, reaction heat removed by reactant --1300--2000bar operating pressur --Higher capacity of .of LDPE product mix than industry competitors in the Americas Autoclave vs Tubular LDPE: • Autoclave LDPE is a more specialty product with broader applications and better margins; Westlake’s focus into food packaging applications provides demand stability. • Supply/demand balance for autoclave grows tighter. Source for both charts: IHS Markit
Low density polyethylene is commonly produced in highpressure autoclaves and tubular reactors. From the 90's on, when the majority of LDPE (60 %) was produced in the autoclave reactors, the tubular reactors gradually got the upper hand. Nowadays the tubular reactor stands for 60 % of the total production of LDPE.Possibilities of autoclave LDPE process Supervisor (Arcada): Rene Herrman Commissioned by: Ismo Savallampi, Borealis Polymers Oy Abstract: This thesis was written to find what different polyethylene plastic variants can be produced in an already built LDPE autoclave. More specifically, the whole process window of the
lames terrasse autoclave
controlled by IR or GC) is compressed by large ethylene/polyethylene system. Hence one has ring-type piston compressors (or packed pis- single-phase bulk polymerization taking place, tons, diaphragm types) in two stages with The mixture is polymerized either in tubular intermediate cooling, to about 1000-3000 atm. reactors or in stirred autoclaves: The detailed stochastic simulation is used as add-on and offers a deep insight into the polymeric microstructure of each macromolecule. Our hybrid simulation approach is applied to high-pressure ethylene polymerization in industrial tubular and continuous autoclave reactors with peroxide initiation. Large-scale tubular reactors with a capacity in the range of 130,000 tpy–425,000 tpy, as well as stirred autoclave reactors with capacity around 125,000 tpy can be used. Description: A variety of LDPE homopolymers and copolymers can be produced on these large reactors for various applications including films, molding and extrusion coating. A commercial low-density polyethylene (LDPE) which is produced by the polymerization process of ethylene in the presence of initiators in a long tubular reactor is the most widely used in polymer .

Product from the tubular process is typically higher in molecular weight and has more short chain branches than LDPE from the autoclave process . Produce LDPE homo-polymers and ethylene vinyl acetate (EVA) copolymers; Source: Echem Enppi, Apr 2013, Polyethylene Production Technologies, via the Internet Archive. Computational fluid dynamics (CFD) is used in this study to model low-density polyethylene (LDPE) tubular and autoclave reactors. A polymerization reaction model is developed using the method of moments. The model includes six steps: initiator decomposition, chain initiation, propagation, chain transfer to monomer, disproportionation termination, and .
ldpe tubular coating
ldpe material types
on low-density polyethylene (LDPE) and linear low-density polyethylene (LLDPE) [1]. LDPE is produced by free-radi-cal polymerization in tubular or autoclave reactors at temperatures up to 300 C and pressures up to 3000bar. The polymerization is started by a thermal initiator like an organic peroxide. By stepwise adding monomer to the
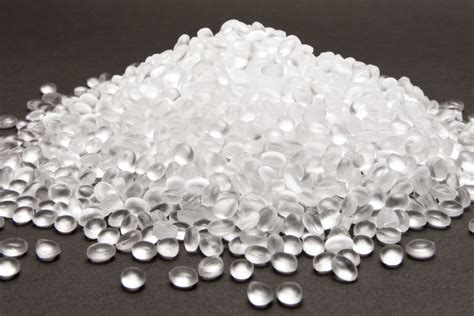
lames terrasse pin autoclave classe 4
ldpe for extrusion
Fedegari Autoclavi SpA, located in Albuzzano, PV (Italy) is the holding .
ldpe autoclave vs tubular|qenos autoclave ldpe